Exactly How Welding Assessment Adds To Durability and Dependability in Fabrication Projects
Welding examination acts as a foundational element in ensuring the long life and dependability of fabrication tasks. By methodically identifying possible problems during numerous phases of production, welding assessments not only stop costly failings however also foster a culture of quality guarantee within the team. Using sophisticated strategies, such as non-destructive testing, facilitates thorough assessments while maintaining material honesty. As projects advance, the impact of these assessments becomes progressively evident, increasing crucial inquiries about their long-lasting advantages and implications for general project success. What particular techniques can be executed to maximize these advantages?

Significance of Welding Assessment
Making certain top quality via welding examination is a vital element of any type of construction job. It offers as a secure to verify that welding processes satisfy well-known standards and requirements, consequently boosting the total integrity of the structure or element being made. Welding evaluation is not simply a procedural step; it is a vital method that assists identify possible concerns early, making sure that they are attended to before they escalate right into considerable problems.
The importance of welding examination can be emphasized by its function in maintaining safety and security and longevity. Bonded joints are typically subjected to severe conditions, and any kind of flaws can compromise the efficiency and durability of the final item. By executing strenuous assessment protocols, companies can guarantee conformity with market regulations, consequently reducing threats related to architectural failures.
In addition, efficient welding examination promotes self-confidence amongst stakeholders, consisting of customers and regulative bodies, that the task satisfies the finest quality criteria. This not just enhances the track record of the fabricator however likewise adds to lasting cost savings by avoiding rework and prospective responsibilities. Ultimately, welding assessment is integral to the success and dependability of manufacture projects, strengthening the worth of quality control in engineering techniques.
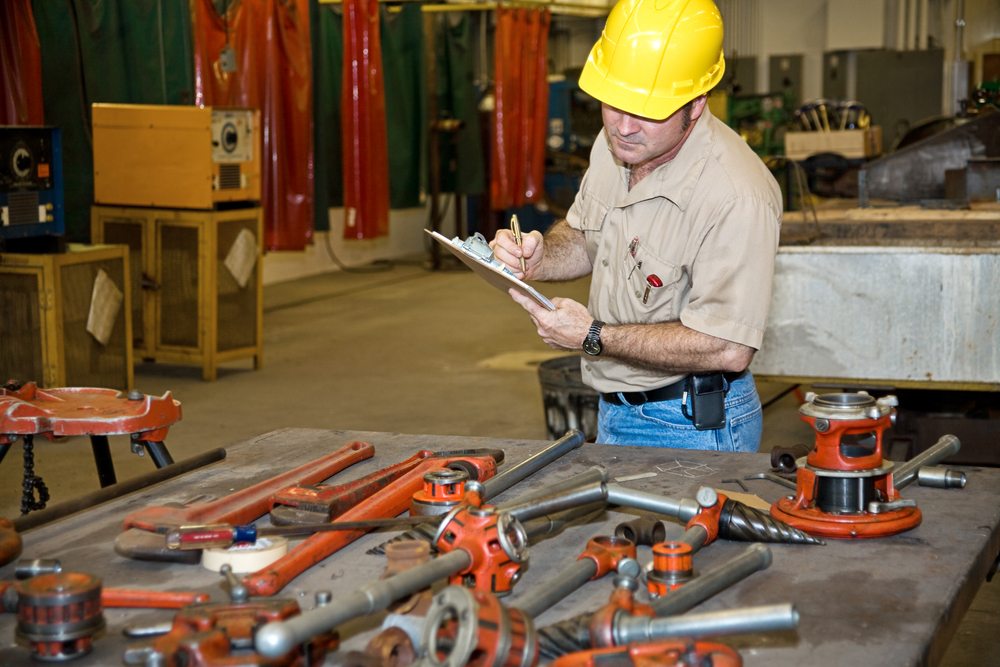
Typical Welding Problems
Welding problems can considerably weaken the structural integrity of made parts, making their recognition and rectification important. Common welding defects can be generally classified into three types: geometric, metallurgical, and service-related.
Geometric defects consist of problems such as undercutting, where the base steel is deteriorated beside the weld, and excessive convexity, which can lead to stress and anxiety focus points. These defects can endanger the stamina and resilience of the weld joint.
Metallurgical defects emerge from incorrect welding procedures or products, resulting in problems such as porosity, where gas pockets create within the weld, and lack of blend, which happens when the weld metal stops working to bond correctly with the base steel. These problems can significantly deteriorate the weld's efficiency.
Service-related defects may not emerge until after the component remains in usage. Examples include breaking due to thermal anxiety or fatigue, which can cause catastrophic failings otherwise dealt with.
Understanding these typical defects equips makers to execute reliable evaluation methods that enhance the dependability and long life of their projects, eventually making certain safety and performance criteria are satisfied.
Examination Approaches and techniques
An extensive strategy to inspection the original source techniques and techniques is necessary for alleviating and recognizing welding issues in fabrication jobs. Different techniques are used to make certain the integrity of welds, including visual evaluation, ultrasonic testing (UT), radiographic testing (RT), magnetic bit testing (MT), and dye penetrant testing (PT) Each method has its staminas and certain applications.

Magnetic bit screening is beneficial for identifying surface and near-surface issues in ferromagnetic materials. By using an electromagnetic field and utilizing ferrous fragments, inspectors can determine suspensions successfully. Dye penetrant screening highlights surface-breaking issues through the application of a dye that permeates right into cracks, making them visible under ultraviolet light.
Using a combination of these methods makes sure a strenuous assessment, enhancing the dependability of bonded frameworks.
Effect On Job Durability
Effective inspection practices significantly affect the durability of construction projects. By recognizing possible flaws and disparities in welding processes, inspections make certain that frameworks are built to withstand functional anxieties in time. When welds are extensively checked out, the probability of undiscovered concerns, which can bring click over here now about structural failures, is minimized.
Normal assessments assist in adherence to industry standards and policies, which are crucial for ensuring the longevity of welded joints. Such conformity not only boosts the stability of the task however additionally guarantees stakeholders regarding the high quality of the work. Moreover, timely detection of imperfections permits rehabilitative actions to be taken early, protecting against costly fixings or complete overhauls down the line.
Additionally, effective assessment techniques foster a society of top quality assurance within fabrication groups. When employees know that their work will be carefully reviewed, they are more likely to stick to ideal practices and keep high criteria throughout the production process. Ultimately, this commitment to quality not only prolongs the life expectancy of the job but additionally minimizes maintenance costs, thus improving the general economic feasibility of construction undertakings.
Enhancing Reliability in Fabrication
Integrity in manufacture is substantially improved with rigorous inspection procedures that attend to prospective weaknesses in welding techniques. Reliable welding assessment not only recognizes flaws early however also gives essential responses to welders, making sure adherence to established standards and requirements. By using non-destructive testing approaches, such as radiographic or ultrasonic evaluations, makers can establish the integrity of welds without endangering the material.
In addition, routine examinations promote a culture of high quality and accountability amongst fabrication teams. They are extra likely to stick to ideal methods and methods when welders recognize that their job is subject to strict examinations. This proactive technique decreases the risk of expensive failings throughout the operational phase of a job.
Inevitably, boosting integrity in manufacture with detailed assessment processes not only increases the lifespan of the made parts however likewise reinforces stakeholder confidence in the task's total high quality and sturdiness. Spending in robust welding inspection techniques is crucial for attaining long-lasting reliability in any kind of manufacture venture.
Conclusion
In recap, welding examination serves as an important part in making certain the long life and dependability of fabrication tasks. By determining defects early and using non-destructive screening methods, examinations cultivate a culture of quality control that complies with sector standards. The organized documents of results not only assists in trend analysis however likewise enhances responsibility and structural stability. Ultimately, reliable welding evaluation techniques reinforce stakeholder self-confidence and considerably add to the useful link economic feasibility of fabrication ventures.
Welding examination serves as a foundational aspect in making sure the long life and reliability of fabrication jobs.Making sure top quality through welding evaluation is an essential component of any fabrication job. Eventually, welding assessment is indispensable to the success and integrity of manufacture projects, reinforcing the worth of quality assurance in design techniques.
A comprehensive approach to evaluation techniques and methods is vital for alleviating and determining welding problems in construction projects.In summary, welding inspection offers as an essential part in making sure the durability and dependability of construction projects.